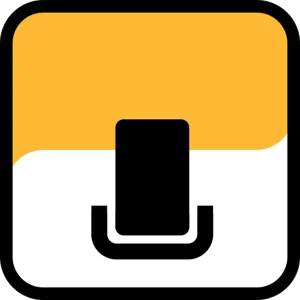
EPISODE 4 | ROI of Innovation in Traditional Manufacturing
We discuss his experience implementing data driven supply chain innovation within a traditional manufacturing environment with real-time goods and asset monitoring; and the ROI of logistics and supply chain visibility for internal and external customers.
- Article
- Transcript
We’re currently working to get the key takeaways for this episode. Stay tuned to Roambee’s Supply Chain Tech Podcast for all the latest episodes to build a more resilient and sustainable supply chain.
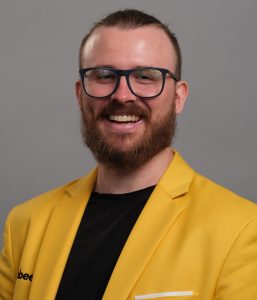
Author
Scott Mears
Senior Marketing Manager
SUMMARY KEYWORDS
Supply chain innovation, data-driven, real-time monitoring, logistics visibility, packaging machines, multi-modal shipping, tracking and tracing, damaged goods, shock tracking, automated shipments, asset tracking, warehouse management, enterprise resource planning, technology implementation, supply chain resilience.
SPEAKERS
Scott Hurley, Florian Birkle
Scott Hurley 00:08
Welcome to supply chain tech podcast with Roambee. In this episode, we speak with Florian Birkle , supply chain management and business analyst at Multivac Gruppe, a leading manufacturer of packaging and food processing machinery. Florian shares with us his experience implementing data driven Supply Chain Innovation within a traditional manufacturing environment with real time goods and asset monitoring and the return on investment of logistics and supply chain visibility for internal and external customers. So how are you today, Florian.
Florian Birkle 00:39
Hi Scott. Nice to meet you. I’m very good. How are you?
Scott Hurley 00:42
Great, wonderful. Thank you for asking. I’m looking forward to your insights. But first, can you tell us a little bit about your background, your role at multivac, and what are some of the challenges that you were trying to solve for.
Florian Birkle 00:54
Yeah. Well, as you mentioned before, multivac is a producer for packaging machines, large industrial machines, for food packaging, packaging of health and life science items, and also in industrial items and products. So yeah, I’m working here since 2015 actually, I started as a working student, and since 2017 I’m working within the supply chain management department as a business analyst. Yeah, I’m in charge of everything data and business analysis within Supply Chain Management, mainly logistics. So warehousing, transportation, yeah, and spare parts, logistics, everything, yeah, around that. And also I’m in charge of some yeah industry, logistics, 4.0 implementations. And I think that’s what we are going to talk about a little bit. Yeah, because of we implemented Roambee tracking and tracing solution this year, and yeah, up until now, we’re happy with it.
Scott Hurley 02:15
Great. So as I understand it, multivac is a global company create these very large food processing machines that you then have to ship all over the world, exactly. Yeah. Is it? Is it multi modal? Is it mostly by sea, by air, by truck? Yeah,
Florian Birkle 02:32
it’s all of that. It’s very multi modal. We ship our machines. They are packaged in around four to up to eight or 10 packages. And then we ship them by truck, by sea freight or air freight, depending where our customer is. We have customers worldwide, as we do have subsidiaries worldwide, and we send our our machines, either to the customers directly or to our daughter companies subsidiaries, where they then get, yeah, maybe something has to be assembled again, and then they go to The customer. We have a lot of intermediaries until our packages arrive at the customers, because we pack the machines here. Then they get truck to a warehouse where they get handled stored. Then they get truck to maybe the port, another part of handling loaded onto the ship. Then we have, yeah, the part of the actual sea freight transport on sea and at the destination port. We have handling again, and so we have a lot of areas and times where something can happen to our shipment, and where we can lose sight or visibility of our shipment, and that was a big problem initially for us, because when the customer or our colleagues wanted to know where is the shipment, when does it arrive in? What state is it, we always had to cycle through this whole loop of information back and forth. The customer asked the subsidiary. They asked us, we asked the carrier, and so forth, and then we had to cycle all this information back, and it sometimes took days. So the information was not, yeah, like not new anymore. Was old information, and about two years ago, we started with experimenting with tracking and tracing solutions, not initially with Roambee, but that then came later, yeah.
Scott Hurley 04:56
Without mentioning specific names. What types of technologies did you experiment with?
Florian Birkle 05:02
Yeah, we first experimented with, like, big, bulky GPS sensors, which you attach to containers, and, yeah, you can then, very low key, see the position and the actually, it’s just the position of the of the good. There were also solutions with which were able to track some shock events or something like that. But everything was very low tech, I would say, not like up to date or state of the art. Then there were also small pieces of equipment which you just attach to the to the packaging, and they track everything that happens. They also track movement, shock, temperature or something like that, but you are not able to see that information live. You then when the parcel arrives, you can then take this small thing and, like, read it, yeah, attach it to a computer and see the information. And that was not helpful either, because there was no what we wanted. We needed a yeah, some live information and yeah, real time status update.
Scott Hurley 06:26
So real time location, condition and information at the package level.
Florian Birkle 06:32
Exactly. Mentioned the package level, that was another big thing, because we with the container tracking thing, there was two not specific enough, because we needed on a package level. Didn’t help that we could track the container, yeah.
Scott Hurley 06:57
Sure, because presumably you’re moving, like you said, three to 10 of these at a time. But at some point they get to a destination and they split up. And at that point, if they’re just trying to.
Florian Birkle 07:07
Exactly, we don’t always have that full container load, where we actually have the container in possession, or we can just attach something to it. We sometimes have less than truck load, or less than container load shipments and yeah, so we need it on this package level.
Scott Hurley 07:25
Can you tell me a little bit about your implementation experience with the real time visibility solution?
Florian Birkle 07:30
Sure. Last year, we did a testing phase over a couple of months where we had some devices, and then, yeah, attach them to some specially picked project, which we had shipments and sent them to our daughter companies. We wanted to have this like, yep, this route where we do have visibility, or good visibility, of our package, so we can track whether the solution is suitable for us or not. So we didn’t like do wild experiments. They will take good care of the package, if you know what I mean, like, yeah, something which we have experience with, and that went very well. And also our subsidiaries, they were very interested very quickly in this technology, because they immediately saw value in it, in the information. And that really was something that, yeah, sped the process up, because then we didn’t have to do, like, a lot of marketing within the company, you know, because always have to, like, sell other people on your idea. But that happened, yeah, quite quickly, actually. So yeah, mid last year, we decided to to go with the solution. And then this year we started, like, really implementing, yeah.
Scott Hurley 09:14
So you mentioned that the value became clear pretty quickly throughout the organization, even the donor company. What are some of the specific aspects of the solution that is driving the return on investment that excited people about it?
Florian Birkle 09:28
Well, we did have some problems with damaged goods when, when they arrived, the damage often was not really, not really obvious. So when we had this change from one carrier to another, as I mentioned before, like from the warehouse to another carrier by truck, usually the second carrier has to check if everything’s all right. So sometimes damage was not. Obvious, and it became quite obvious when we had shock tracking, so we could actually see when something happened to one of our packages and where it happened. So the whole discussion of who did what to our package became, yeah, somewhat very easy for us, because we could, like, see it and show it. We had a timestamp, we had a location, and we had Yeah, Qi powers that we could show and yeah, that level of information was something we never had before.
Scott Hurley 10:38
So have you been able to use this information in the aggregate to start to benchmark the performance of transporters or to evaluate the various lanes that you manage to see which ones are performing best and which ones you need to monitor for damage more often?
Florian Birkle 10:56
Well, we now have information that supported some of our thoughts already, because, of course, the lanes which had the most handling processes involved are the lanes that are most prone to damages. So that became obvious. Then also, what we found out rather quickly was that we told our carriers that we are tracking the shipment, because, yeah, we wanted that visibility. And also, I mean, sometimes the packages get checked and then they see it anyway, because batteries involved and stuff like that. So yeah, we told them and telling them already, we felt that they were handling our packages more carefully. It was a Placebo Effect.
Scott Hurley 12:09
That’s interesting. So what do you think is next for you in terms of progressing along the journey of what your goals are for supply chain logistics, and whether it’s a building scaling up with with real time visibility, or what other aspects of technology are you excited to evaluate and implement.
Florian Birkle 12:32
What we are doing with the tracking and tracing solution as that there is A Roadmap actually, we want to make the whole process of setting up shipments and, yes, setting the whole thing up more automated. We have, of course, warehouse management system and enterprise resource planning system, and we want to hook, yeah, those technologies up together, and then it would be perfect if, like, the the shipment in the portal would be generated automatically when we package the shipment in our packaging department and everything’s like, yeah, totally automatic. That would be great. And we’re working on that. Sure, there have to be some process adjustments, and we have to link the correct data and everything, but that’s what we’re doing next. Okay, yeah, and well might also be that there is some asset tracking in the future, because, of course, we also have a lot of, we don’t own trucks, but we have a lot of machinery driving around, like forklifts and, yeah, yeah. Also like technician cars for maintenance, so there could be some some asset tracking. And, I mean, I know there’s a solution for that as well, right?
Scott Hurley 14:14
Absolutely, yeah. And you had mentioned the fact that multivac creates these food processing machines, but also some medical devices and other goods. Are you considering expanding it across the suite of goods as well?
Florian Birkle 14:33
Well, not that it’s packaging machines for medical goods. Okay, that was what I meant. Yeah. So, well, the solution is basically for any, anything that we package and ship to to other destinations. So, yeah, of course, we’re trying to expand. We actually we’re right now. Have a experiment that we’re doing, or little, little test, we’re sending two of our machines to different subsidiaries for training purposes. Usually, the technicians come to to the headquarter here to get training once or twice a year. And because of travel restrictions right now, we are sending the machine, and we’re actually tracking it on the way with our tracking and tracing solution, yeah, to know where it is. And to always know the state the machines are in. So these are these little side projects that are possible with this solution, because it’s very uncomplicated.
Scott Hurley 15:56
Okay, any parting thoughts before we wrap up?
Florian Birkle 16:01
I think we found a great solution. I’m really happy with it, actually, and no, I’m thankful that we could speak to each other. Was my pleasure actually.
Scott Hurley 16:12
Wonderful. That’s great to hear. Thank you so much. Florian, appreciate your time. Thank you. Thank you for tuning in to this episode of the supply chain technology podcast, please check out the transcription and other episodes in the series on this page.
Scott Mears 16:26
Hi, my name is Scott Mears, and I’m one of the hosts of the Supply Chain Tech Podcast with Roambee. On this podcast we talk to supply chain heroes from around the world about everything, ranging from the disruptions related to supply chains, their personal experiences with tracking technologies, strategies to build resilience, and much, much more. We already have some recommended videos for you to the side of me, and if any of this sounds interesting to you, do subscribe to our Youtube channel and hit the bell icon so you don’t miss another Roambee video. I’ll see you next time.