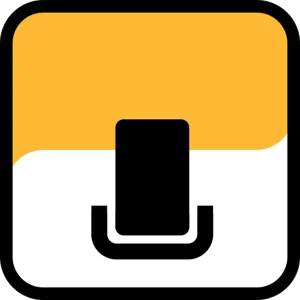
EPISODE 16 | Sensor Solutions Confront Pharma Challenges
We discuss the challenges that confront pharma cold chains and how real-time visibility data can reduce the risk. With the COVID-19 vaccine distribution endeavour underway, Brett’s insights on pharmaceutical cold chain are timely and valuable. With many years of experience in quality, as well as in the supply chain side of pharma, Brett explains how teams can come together to deliver on time and in top quality.
- Article
- Transcript
We’re currently working to get the key takeaways for this episode. Stay tuned to Roambee’s Supply Chain Tech Podcast for all the latest episodes to build a more resilient and sustainable supply chain.
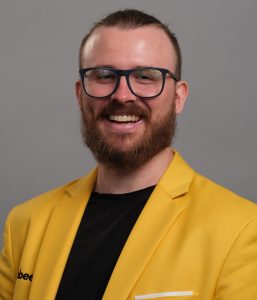
Author
Scott Mears
Senior Marketing Manager
SUMMARY KEYWORDS
Pharma Cold Chain, COVID 19 vaccines, Quality Assurance, Supply Chain, Distribution, Temperature Monitoring, IoT technologies, Real-time Alerts, Data Integrity, Passive Data Loggers, Geographical Challenges, Infrastructure, Compliance, Predictive Capabilities.
SPEAKERS
Scott Mears, Brett Marshal, Premsai Sainathan
Premsai Sainathan 00:08
Welcome to the Supply Chain Tech Podcast with Roambee. In this episode, we dive deep into a topic that’s been widely discussed because of the COVID 19 vaccines. It’s nothing but Pharma Cold Chain Management we have with us. Brett Marshal from Zuellig Pharma to explore this topic. Brett heads Zuellig, Quality Assurance practice, but moreover, he spent a lot of years managing supply chain and distribution in pharma to provide us with a holistic picture. Brett, welcome to the podcast. It’s a pleasure having you here. I’d like to begin with my first question to you. You have spent a lot of time in the pharma quality and distribution space, so what got you into this? And what do you really like about your work every day?
Brett Marshal 00:54
Thanks, Prem. So it’s I think when I left, left high school. Actually, I was a frustrated vet, like a few other friends that I had at the time, but I finished up studying Transport and Logistics Management at RMIT and and it, I sort of found that that it was an industry that I really enjoyed working in I worked with Lynn Fox to begin with in Australia, so I got my cut my teeth in the business, in transport, logistics and and I think, you know, as a career, it’s been fascinating to be able to move through different disciplines within the area of supply chain, and also to be able to work across different parts of Australia. And then when moving into Asia, I’ve I’ve lived in in Indonesia, Thailand, Bangladesh, Philippines and Singapore and and worked in different roles in those countries as well. So I found it to be an extremely challenging area to work and pharma, especially with with the quality space that I’ve been working for the past few years, is a particularly interesting area to work very rapidly changing and and to be able to, you know, put in place a quality management system and and have oversight of a quality management system for products that you know are going to be used in the treatment of patients, is a really important, really important role. So I enjoy what I do, and I enjoy, you know, the oversight of of the business and the team that works with me, and enabling that team to be able to do what they do in the quality space as well.
Premsai Sainathan 02:50
Thank you, Brett. Brett, my next question to you really would be around the COVID 19 scenario, as we all know, the COVID 19 vaccine has actually brought out the pharma cold chain into the mainstream, right? So all of the challenges that come around shipping in a cold chain environment, especially when it’s shipped to parts of the world where people are not used to first world cold chain management techniques is being talked about. Brett, you have spent a lot of time running and managing large cold chains. So can you tell us a little bit about some of the scenarios that contribute to this risk that’s being widely discussed?
Brett Marshal 03:34
Yeah, I think that working in Asia, as we do, and the business that we have covers 13 countries across Asia, and many of them, you know, like the Philippines and Indonesia, are obviously geographically quite diverse. And I guess you know, one of the major challenges, you know, for farmer distribution in general, is probably the quality of the infrastructure that’s available in each country, and that can be around the ports of entry, with with airports and with seaports and and then the in country infrastructure, around road systems, and, You know, sometimes the the potential for disruption through the impacts of climate, with floods and typhoons and those types of things. So, you know, we have to design, you know, our infrastructure and our systems to be pretty robust to deal with those types of things. I think certainly, you know, COVID and you know the supply chain impacts has certainly brought, brought supply chain to the front page and into the broadsheet. But I think from a farmer perspective, you know, we’ve been operating in Asia for nearly 100 years, and. And certainly in that time, we’ve built a pretty robust system and compliance to international standards. So we do handle a significant proportion of vaccines today, and I’d say that, you know, we we’ve seen evolutions in terms of the storage infrastructure available and the packaging systems that are available, the the the devices, the temperature monitoring devices that we use to give us visibility of of temperature. And you know, how we integrate these, these components into an ecosystem which provides the right storage, the right storage, temperatures and maintains those through to to delivery to the patient. I think that certainly the geographical challenges are probably the the ones that that have been the biggest to overcome in the past. But you know, certainly the development of, as I say, packaging systems, passive packaging systems that we’ve seen in the last 5-6, years has really improved capabilities in that respect. And so, you know, the the ability to maintain temperatures within specification in the past, with with packaging systems, would be 36 to 48 hours. But today can be 96 to 120 hours. So you know, the technology has had a big impact. And I think that’s helped to secure the provenance of the product, to to hospitals and pharmacies and drugstores and that sort of thing, and then to the patient.
Premsai Sainathan 06:52
Brett, if I was to visualize the entire supply chain for this distribution of vaccines, what are all the places where things could go wrong, or maybe Murphy could happen? You’ve spent a lot of time here, so I think you must have seen a lot of practical scenarios, and you would probably be well prepared to address them before even they occur. But for somebody who is learning the pharma supply chain, or who is from another industry, what would those scenarios be, or where, what are those risk points in the supply chain?
Brett Marshal 07:34
Yeah, I touched on on the risk areas of ports of entry, so airports and seaports, particularly for those countries that are geographically diverse as I mentioned, so Philippines, Indonesia, Malaysia, I guess, where there are situations where the product can be exposed to extreme temperatures during loading or unloading. And you know, sometimes in the case of refrigerated containers in shipping ports and the disconnection from power, sometimes you can get situations where that that takes longer than than it should. And so we can see, see deviations occur because of the the power disconnection. But I’d say that when we look at international ports, airports and seaports, the international standards have have improved to a point where the risk has been very much reduced in in many of the airports that we that we operate, or that operate in the countries where we are today, and many of them, many of the airport management managers and the airlines have also improved their standards become aligned with quality standards, like IATAs CIV quality certification. So that’s that’s helped to address the inbound risk, I guess, where we’re doing branch transfers, we still have some, some some areas of risk, and that’s one of the reasons why we’ve we’ve been helped with the improvement in packaging systems to address those key risk areas, I think, also in in handling, you know, the the storage infrastructure that we have, the packaging systems we have, it’s important that we give the right level of education and training, to to to the to our teams that are involved in working with those in those areas and with those components, preparing those components for for packing and shipping, that everything follows, you know, the required procedures. From pre, pre-quality preparation of ice gels or the the PCMS that we were using, right through to the way that the pack out is prepared prior to putting product into the temperature control packaging system, and then how that’s packed, in terms of the delivery vehicles and then transported. So the training processes and the guidelines and the SOPs that we put around that, and the way that we manage the teams that are involved in that process is pretty important, and those are probably some of the key risk areas that that we see.
Premsai Sainathan 10:47
Brett you touched upon temperature monitoring devices. So the pharma industry is very, very familiar with data loggers, and it’s been treated as the gold standard in pharma cold chains for decades now. So do you think it continues to solve the problem that you’re talking about, or is it time for the pharma industry to look beyond just passive data loggers?
Brett Marshal 11:18
Yeah, I think, certainly, the passive devices that we’ve used in the past have have given, you know, where, where situations are good, where, where we have validated packaging systems and validated transit lines that we use. You know, the the data loggers have the capability to confirm that that we have the correct systems in place, but it’s, it’s always a retrospective review from a passive device. And I guess, as an industry, we’re looking to to identify ways to become more proactive and more more capable of preventive management. And so I think this is what’s pushing an increased focus on, how do we move to real time capabilities for alerts, not not so much real time data capture, because that’s part of a normal part of a passive device, but real time alerts or an increasing an increasing availability of integrations with IoT technologies to be able to speed up the alert alert receiving process, which allow, may allow some form of responding action as part of a shipment. So I think, I think certainly that that penetration of IoT, the penetration of the growing capabilities of of real time alerts. That’s that’s kind of the base improvement in in the device. I think the communications technology to support the use of this equipment is also important. So we’re starting to see improvements in in telecoms infrastructure around the region that are helping these systems perform better. And I think you know, real time alerts will certainly, or the ability to to generate real real time alerts will will help enormously to reduce quality risk. I think also, the ability to capture the data and use the data is probably an area of greater focus than it was in the past. And I think traditionally, device providers had their data capture platforms, which were pretty much proprietary to the to the devices, but we’re starting to see the ability to have more agnostic data capture platforms that then can be integrated back into, you know, in our as in our situation, the the business support platform that We have in place, you know, being able to capture that data and download that data directly.
Premsai Sainathan 14:27
Brett, you obviously must be having some experience, you know, working with some of these IoT and, you know, data platforms. So what do you think is working today in terms of technological capability, and where you see that some of these technologies need to evolve.
Brett Marshal 14:50
I think we’re still at the the fairly early stages of integration with IoT and, you know, the ability, as I was talking about earlier, the ability to generate those real time alerts, I think, you know, in the past, devices have been a balance of, how do we have enough battery, you know, battery power to be able to sustain the device, versus how do we capture data, versus how do we transmit data? And there’s been a little bit of a battle between those three, those three requirements inside, you know, the confines of the device itself. But I think technologies allowing battery sizes to and power to to decrease in size and transmitting data, transmitting capability to to improve, and the ability to access the cloud directly is reducing the requirement for data capture within the device as well. So I think you know the these are some of the the tech evolutions that we’re starting to see. It’s always a little bit challenging to get through the qualification and validation process of these devices, which in pharma, is a really important step prior to really operationalizing the use of devices and data capture platforms. It’s a requirement that has kind of carried over from Good Manufacturing Practice in the manufacturing side into good distribution practice in distribution so, so where we’re at, at the early stages of, I think the next, the next step for for devices and the use of devices, and then I think, as I mentioned, the future will be, how do we start to to more effectively use that data, and how can we more effectively integrate that data into other data systems or data pools that we have available.
Premsai Sainathan 17:04
Brett, this brings me to actually two interesting questions about what you said. So one is, you’re talking about these sensors and the platforms. What are some of the pharma regulations that these technologies need to comply with before they come to a pharma user like you, or any, any, any pharma company. For that matter, my second question is around the data capabilities that you talked about. So one is, one is the sensor data, but what other data sources are really important for you to visualize what’s happening to your shipment or your distribution lane in real time.
Brett Marshal 17:52
Yeah, I think in terms of the quality, quality requirements around the devices, I talked a little bit about qualification and validation of the devices, and also the the calibration of the devices so they they need to be able to perform within very specific requirements. The you know, the temperature ranges that they’re capable of measuring must be within, within very strict specifications. The minimum period of time between data being logged is is fairly tightly specified.
Premsai Sainathan 18:38
And for your for your last mile deliveries right, where you cannot have a blank spot?
Brett Marshal 18:45
No, that’s right, and particularly important. Even as we review data from a data integrity perspective, that that there are no gaps in the data, that that that we have a consistent record of temperature right right through also, as you know, we download data from devices, and again, related to data integrity, we need to make sure that there’s no opportunity for any of the users of the system to be able to manipulate any data, and that it remains, the integrity of the data is maintained right through the process as well.
Premsai Sainathan 19:29
Are there any certifications that come into play here which give that confidence to the pharma industry? Sorry, any are there? Are there any kind of certifications that come into playbreak which give that confidence on these IoT sensors to the pharma industry?
Brett Marshal 19:49
Yeah, so in most cases, we require a calibration certificate to be supplied with the devices, and this can be quite challenging to. Find whether the manufacturer themselves is going to provide the calibration or whether the calibration needs to be performed within the country where we’re operating, but in many cases, it’s the manufacturer themselves that are providing the calibration certificate and recertification is usually on a minimum of an annual basis. So this, this process needs to be considered from a cost perspective as well, because it’s it’s not always cheap, yeah, in many cases, it can be cheap, actually cheaper to buy a new device than it is to to have the device recalibrated.
Premsai Sainathan 20:42
Yeah. Yes, and Brett talking about the second piece, which is about the data. What are some of the data sources that you’d like to see that he spoke about, which is beyond just temperature, which is coming from the IoT senses?
Brett Marshal 21:00
Yeah, I think that, you know, as we look at initiatives that are being launched under industry 4.0 and supply chain 4.0 and quality 4.0 we start to see a broader integration to data sets that come from, from, you know, the company’s business platform, and also external data sets that might be from, like unstructured data from a from an EQ ms, An electronic Quality Management System, or potentially from from other information sources, such as such as natural disaster monitoring sites or temperature and humidity monitoring sites, anything that can kind of impact the potential condition of the delivery process can also be quite helpful. And I think being able to integrate that data and then be able to use some of the tool sets from artificial intelligence and machine learning and robotic process automation to start to improve predictive capabilities and and, I guess when you look at the analytics maturity curve, how you can push the organization up the maturity curve through predictive to prescriptive and into cognitive, analytical capability that gives you a much more effective risk prevention capability. So I think that’ll be the future. You know, there’s, there’s a lot of integrating platforms that are, or integrating software that’s, that’s also being made available from a number of different suppliers, but I think it’ll take some time to build out that capability.
Premsai Sainathan 23:03
Absolutely. Brett, and I think what you’re really driving to hear, which is very interesting, is that the time to react, it seems to be very critical for you, because what you really want is you want the system to tell you what I should do without having to figure out what this particular temperature excursion, for example, means. You want to know what’s that a temperature excursion is happening, where it’s happening, what is probably causing it, and who I should contact in my chain of custody to actually rectify it?
Brett Marshal 23:39
Yeah, exactly. And it’s really it’s moving from the corrective approach of the past to a more preventive capability in the future.
Premsai Sainathan 23:53
Yes, let me shift gears a bit, and here’s something that I observed about your about your experience. You’ve actually worked with the quality side of things, and you’ve worked with the distribution side of things a lot of times. I learned that these two departments have a lot of tussles, because one is trying to improve the quality of the product and spend more on it, while the other departments trying to typically optimize cost find more cost effective methods to get the product across from one area to another. So how have you been handling some of these conflicting priorities? I think since you’ve been part of both these teams, we could get some insights from you here.
Brett Marshal 24:48
I think that’s a good question. I think, you know, the the role of quality is particularly important and and it’s, it’s, I think I talked right at the start about a. Quality Management System and and quality’s role in in the governance of a quality management system is to be able to interpret, interpret change that’s, that’s that’s being pushed through the system from regulatory change or supply chain change or technology change and be able to build that QMS in a way that the operations team are going to be able to adapt to the required changes most easily. I think the traditional view of quality is, has been as a policeman, and that’s because, you know, we’ve, we’ve seen a highly operational nature of quality and, and what we’re trying to do is to kind of build a more effective quality culture through the organization, to bring quality back into its role as as governance and and looking at quality assurance, rather than being directly involved in the operational side. And give the process owners more responsibility for, for the way that they’re they’re managing their their process. I think that that, you know, when we take quality out of its functional silo and we start to embed it at the start of end to end scenarios that we’re looking at from a from an operations perspective, we get a better result. You know, in the manufacturing sector, they talk about quality by design, and I think that’s that’s what we’re looking at to kind of build to to break down the potential conflict scenarios by building pro quality into the process right at the very beginning. So there’s an ongoing process of review from a quality perspective, right through the delivery of changes that we might make to infrastructure or systems or technology or process. And you know, when we look at it from that holistic perspective, and we implement from from a holistic perspective. It takes the conflict out, out of the scenario. And I think that, you know, through the COVID period we’ve probably seen, you know, we talked about how supply chains have become much more prevalent and much more obvious to to the general public. I think also that when we look at quality practitioners of the future, they’re going to need to be able to have a skill set and an understanding that includes supply chain capabilities and and even technology so familiarity with, you know, the the attributes and the components of digital transformation, because to be able to build and manage the quality management system in the future, they have to have that understanding. So no quality person is going to be purely quality in the future. They’re going to have a range of skills that that help them to manage the quality of the business most effectively. And I think when you can understand both sides of the discussion, it really helps to reduce the potential conflict.
Premsai Sainathan 28:30
Excellent, Brett, that’s very insightful. Because, like you said, quality has always been viewed as the policeman. Is there any example you have where you’re able to describe this change, something that you’ve come across, where quality has actually been working hand in hand in designing the distribution process?
Brett Marshal 28:56
Yeah, I think that, you know, one of the things that we look at is in, you know, typically we have metrics around non-conformance and deviations that might occur. And, you know, we look at the trends of data that we have on monthly, quarterly, annual basis, helps us to identify specific risk areas. And a part of our part of the work that we do with the operations team is to identify specific projects for improvement and and teams that are made up of both quality and operations people are using the data that we’ve taken from, you know, from the non conformance risk analysis and using that to build a project to to improve whatever contributing factors we’ve identified through that risk analysis and and proactively address that for the future. And we’ve seen that work very, very successfully. And. And there’s a number of projects, you know, around operational readiness and also in situations where we’re performing secondary repackaging, and, you know, changes to the production processes that that improve output and quality of results. So there’s been, been a number of examples where we’ve seen that work effectively.
Premsai Sainathan 30:25
Excellent. Brett, thank you so much for sharing your experience with us. If there’s one thing that you’d like to leave the viewers with in terms of a message as a pharma professional working on quality and improving distribution at this critical time. What would that be?
Brett Marshal 30:45
I think, you know, we we have a very important job to do in in terms of of the way that we manage product, the integrity and the quality of the product, to ensure that that patient health and safety is maintained, and that’s a key objective for us at all times. I guess in these COVID times, there’s certainly a huge focus on how COVID vaccines will be managed and and how they will get to the to the required populations in the different in the different geographies. And that’s that’s an extremely important priority for for us as an organization. But I also think that, you know, we have the existing base business which needs to continue to operate, and we have, we have a need to continue to serve the patients of with with the products that they’ve used in the past and will continue to use in the future. So I think, you know, it’s, it’s how we continue to to perform our role. You know, we’ve, we’ve overcome the challenges of of COVID in many ways, and we have a very robust operating model. We make sure that that we look after our people and our systems for the future to be able to maintain that capability.
Premsai Sainathan 32:18
Well said, Brett, thank you so much again for participating in this tech podcast. It’s very insightful to me, at least. And I think all the pharma supply chain professionals, quality professionals, and even supply chain professional outside of Pharma would have got a lot of insight into everything that you shared about technology, about quality and distribution, working together, and your experience of all the risks that need to be mitigated in advance in this critical supply chain, which caters to patients around the world. Thank you. Brett, it was wonderful having you.
Brett Marshal 32:57
Thanks. Prem.
Scott Mears 32:59
Hi, my name is Scott Mears, and I’m one of the hosts of the Supply Chain Tech Podcast with Roambee. On this podcast we talk to supply chain heroes from around the world about everything, ranging from the disruptions related to supply chains, their personal experiences with tracking technologies, strategies to build resilience, and much, much more. We already have some recommended videos for you to the side of me, and if any of this sounds interesting to you, do subscribe to our Youtube channel and hit the bell icon so you don’t miss another Roambee video. I’ll see you next time.