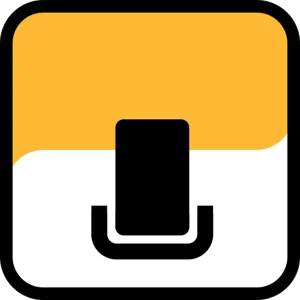
EPISODE 18 | Latest Tech for WIP Inventory Monitoring
We discuss about how you can use technology to monitor Work-In-Process Inventory in large manufacturing lines like his.
- Article
- Transcript
We’re currently working to get the key takeaways for this episode. Stay tuned to Roambee’s Supply Chain Tech Podcast for all the latest episodes to build a more resilient and sustainable supply chain.
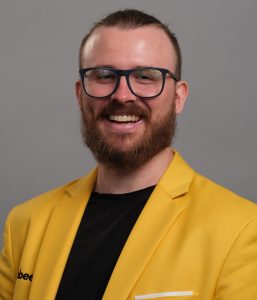
Author
Scott Mears
Senior Marketing Manager
SUMMARY KEYWORDS
Supply chain visibility, manufacturing, customer centric, logistics challenges, BLE tags, data analysis, product tracking, custom orders, delivery schedules, manufacturing process, sensor technology, work capital, quality assurance, safety issues, digital transformation.
SPEAKERS
Marco Aurelio de Andrade, Premsai Sainathan, Scott Mears
Premsai Sainathan 00:08
Welcome to the supply chain tech podcast with Roambee. In this episode, we speak with Marco Aurelio de Andrade. Marco is the customer intelligence analyst at Gerdau Summit, and he talks to us about how you can use technology to monitor working process inventory in large manufacturing lines like this. Mark, welcome to the podcast. Such a pleasure having you here. I know you are and I know you are actually spearheading phenomenal project around manufacturing, supply chain visibility at your company, and there’s a lot of value that you’re deriving from it, which we would like to dwell into in detail here. So Marco, before we begin talking about the project and the value and how you went about implementing visibility. Can you understand a little bit about your role and what Gerdau does in Brazil?
Marco Aurelio de Andrade 01:09
I’m a mechanical engineer, but I don’t actually my fault. My work focus is a little bit twisted from a mechanical engineer. It’s I work with innovation and data analysis and developing developing apps, developing software inside the summit, you know, Summit. It’s one of, again, outside in Brazil. And as you know, Gerdau is a major city, theological leader in Brazil. In the world. We have a lot of meeting milling operations around the globe nowadays is mainly focusing in the America, the Americas. But again, also it’s, it’s a joint venture with Sumitomo Corporation from Japan, as well as with JSW, Japan Still Works, and we focus along tested and forging products like big products like renewables. It’s a big, considerable product that’s, it’s used for the rolling use. In the rolling use, it’s, it’s, it’s main responsibility is to to confront it mechanically, the the steel, to become an end product, to be consumed as a as a commodity. So we produce, besides rolling new rows, we it’s a so Exactly, they are big assets, right? They range from 500 kilograms to 60,000 kilograms. So we’re big, big products, like two meter diameter, your cylinder, electrometer diameter, and five meter long. So and we also products parts from the for the wind, for the wind winds turbines, like we produce rings to make the bearings from the the berries that they are inside the the windmill. So mentally, big products and being heavy products, if we are one of difficult to in the logistics areas, there are big challenges in there.
Premsai Sainathan 03:45
Marco, that’s very interesting, because every time you know you talk about manufacturing, people always think that there is not so much of high tech technology used in supply in the Supply Chain side of manufacturing. Of course, you know manufacturing has already gone through that automation wave and maybe what Gartner calls as the hype cycle, but today, when it comes to the supply chain side of manufacturing, which is within your facilities, as well as outside your facilities, you seem to have invested in technologies to gain visibility into your supply chain, which includes your working process, which includes your job progress tracking. So could you tell us a little bit about what motivated you to explore visibility within the manufacturing facility, as these manufacturing components go through different stages.
Marco Aurelio de Andrade 04:55
You know, since we produce big, big products. And our products are not shelf products, they are each each customer has its its own product. It’s they are very custom made products. So having the visibility of them across the society is essential, because they are. They’re not only one product line. It depends on the customer needs that we are mainly customer centric company. So the customers are our business, you know. So we need to have the control of our products in the tip of their hands because of their the schedule of the deliveries from our customers. They since we are entering a new market style, the time to provide the products for our customers. It’s really critical for the customer services.
Premsai Sainathan 05:58
Interesting. So this is actually coming out of the fact that you really want to stay committed to your customers on the timeline that you offer them. So is this like a make to order model that you follow with your customer? So the customer places an order and then you begin manufacturing the product to suit the customer specification, and typically, how long does it take for a customer to receive their product from the time that they place an order.
Marco Aurelio de Andrade 06:33
It depends on the customer needs. Sometimes they are they have a critical they can they have a critical they, they can have a critical piece that it will affect its operation. But can say from started to manufacture to the end the product needs takes around from one month to three months depends on the product line,
Premsai Sainathan 07:07
Interesting, and in this time frame of one month or three months, what are all those things that can possibly go wrong, which kind of increases This timeline or keeps the customer waiting?
Marco Aurelio de Andrade 07:21
You know, since, since, since our opens are big. Our process time are big. You know, Premier and history, 20 process. There are some kinds of cycles that takes almost months to complete. So some small delays on preparing a batch for the process are really critical. You know, if you you need to prepare a batch with pieces one, two and three, you know, you can’t find the second piece. It’s a major issue. You’re delaying. Not only one, one, if you delay, is the whole batch.
Premsai Sainathan 08:04
Interesting. So what you’re saying is, so you have an order, and then you have multiple components that comprise that order. And if you cannot find all the components that go into that order, you’re probably just maybe it’s you found 99 of those components, but you still have that one component which is remaining, but that’s going to actually delay the whole order and the onward shipping the customer.
Marco Aurelio de Andrade 08:29
Yeah, bigger products, bigger problem. When the products increase in size, it has a lot of logistic problems to start it within the process. Then, you know, sometimes you have, you have a huge size. So because we have to start big products and distributes, we think you can just start it in a shell. It’s not a simple product you have. You have even safety issues about the the storage of these products, right? You can just put it right besides on another because it’s the cylinder, the huge cylinder of 20,000 kilos, if it’s it starts rolling, then it says it’s a huge security issue. So when you’re dealing with this kind of logistic problems, we have to know which, where, which, what our product is with certain kind of reliability. Not only just start, this product is in this buffer. So I if I have, if the logistic operator have to reach for the products that’s behind it. It has to move, to move the product, the interior product. Then, if you were just relying on paper or just the memory of someone when you will be on. This kind of logistic operation, you you need to depend on something else. You have to implement technology. You have to improve the control of the the logistic data so yeah.
Premsai Sainathan 10:23
Marco, so what you’re telling me is that even if you’re using you know digital systems, right, not knowing where that particular component is or the sub assembly is is going to affect the fact that somebody has to actually manually go look for it, and sometimes that also means moving things around. And, you know, a lot of unproductive time that goes into that, and that’s why you chose to monitor your job progress and all the components that come along with it. So how is this your visibility journey? For you, I’m sure it must have taken some time for you to evaluate the different types of solutions available and identify what works, what doesn’t work, and so on. So could you tell us a little bit about that journey to identify the right technology that will do the job, to get visibility in your job, progress monitoring use case?
Marco Aurelio de Andrade 11:33
Okay, when I started the journey, which was more than one year ago, I just, I was dependent on market full of IT solutions. You know, any consultant company could that, we might say, Oh, have you tried the ref IG? It’s many years. It’s a big it consumes a big part of the market, but it’s kind of antique technology, you know? It’s I heard from Intel a long time ago, so I want to study it, right? So I one of the first problems we watched over because the interference with metallic products. So the first case, if we fix IG tag on products, it wouldn’t need to be the cheap, the cheapest and most standard one, which would have to be have a special coating. And then we went after we evaluate that it’s in the nature of the RPG. We just don’t kill the major problem, right? Because you just pass through gateways, and then we scan about with it. And if you if you lost the visibility of the gateway, you still need to allocate someone to go to the site with a collector and start scanning, so it’s not an active kind of monitoration. So I have conflict with another kind of technologies I also saw about tomorrow. So it’s sucked, but the sensor, it’s it’s really, it’s not only for localization, always, it has different kinds of purpose. On the tracking device. It’s like it has a lot of potential. You know, it’s fantastic kind of technology. But it’s over. It’s over about further, the product, the process we have to to, the problem I have to solve, right? And so we kind of look at that also to be only now. It’s like a simple protocol of communication. It’s less data we need. It’s like a cost, wiser and the size. It’s really critical for us. You know, if you want to implement a lot of talking device, talking device to communicate with the network, it would have been become much less the size of my hand with a huge battery. It is consumes a lot of resources that we just really don’t use it. This doesn’t, doesn’t match the the requisites of the product, the project. So we decided to study a lot about BLE since it’s resource wise, about battery, about size, it’s really critical for our process. Because. Uh, how do you have another problem is, how do I put the tagging on my products? It’s really critical, because it’s like a really big slab of metal, you know, really hazard those environments with a lot of dust. It’s a base industry, you know it’s like with high temperature is not suitable forever for not devices, not fragile devices. So it has to try this with BLE. So to solve a problem,
Premsai Sainathan 15:41
And these BLE tags, when do you actually put them on the asset? And when do you take them off?
Marco Aurelio de Andrade 15:50
We take them off from the when we will ship it to the customer. So the final process, when we are shipping it to the customer, we remove the tag and to insert in the process, we we decide early on not on the first process, because it has the elaboration of the liquid metal, so it’s not possible to start there. But after the products take its first shape, and it’s cool down, and then it’s able to start being monitored.
Premsai Sainathan 16:29
So by inserting the sensor, you are able to watch every product which is part of that order, go through your entire factory premises and give you live status updates on where this is at what point in time, and if it’s sitting there for too long, if it has missed a particular process. So not only are you able to move this faster, but you’re also able to ensure that this is actually gone through all the stages in your manufacturing process.
Marco Aurelio de Andrade 17:14
We don’t, we don’t implement the discrete phase of the process because, you know, it’s, it’s really small, small areas. We are kind of not mature enough in the project to go to that grain of of detail. You just like I was seeing beers, because, you know, other process doesn’t happen in the well defined line. So it will be effective to determinate a zone for each work center. So we zones of work centers, you know, because one machine that is, it’s besides one another, one another. They do different kinds of operations in the process, but they are really close within each other. Like within 20 meters, you have two machines that do different kinds of processes over there vertically that they are have each one have is small contribution to the product. But from a higher perspective of bigger parts of the process and all and we can have the the visibility of the idle time of the the this kind of product, you know, so we can supply our SOP sector to detail the size, not just relying on appointments from the MES solution.
Premsai Sainathan 19:02
Interesting, so you’re actually able to match your SOP with the actual moment, or the trail or this product actually takes across your factory and reduce the idle time in the process, which again translates to a quicker order delivery to your customer so that you can keep up your commitments.
Marco Aurelio de Andrade 19:23
This final objective, but we are, we’re starting to generate it right? We we implemented in different phases because we have different products. John, not just only only rolling your rows. We have rings and toilets leaves and main shaft. So each one has its kind of engineering problem to, how do I fix the tag in the the products? How do I train our operators to to do the, do the the operation of the system? How to does he register a new asset? How does the logistic sector don’t register? So we are just doing phases. After all these phases are complete, we will start acting on the SOP projects and all my parts. So we have now the data, what we will generate from it, and then we, with this kind of data, we will do another phase and fail. How do I we have then stage this to the customer? How do I bring this kind of value to our customer, right?
Premsai Sainathan 20:41
Absolutely. And Marco. That brings me to my next question, which you just touched upon data, right? Which is exactly what is the most valuable asset that’s coming out of all of this visibility and sensor implementation that you’re doing within the factory? Can you tell me a little bit about the kind of kind of value that this data, data is providing to you or can provide in the future. What’s the kind of analytics and reporting that’s of most interest to you from the data that’s coming out of monitoring all of these assets in your facility.
Marco Aurelio de Andrade 21:22
Data is like, I’m a data analyst, so I brief this every day, and we are still generating data, but while we generate it, we will, will have an wishlist of analytics, right? We will start. We will we already think of the end of journey, right, and on one of the most valuables visualization products that we will generate the future are the the weak products, you know, and how much we buy each kind of products, wine, we have active in our society, or in which, if the stage of the process, it’s Seems it’s everything. So we can have a detailed, detailed view of our working capital. We really detail, not depending only on, on MRP or MS systems. We have no we know that this, that piece is this number, and it’s, it’s linked to the MRP. To watch over the detail costs. So it really needs the information from us, from the physical side to the digital side, the judicial data. Now the visibility is the main hook from the digital to the to the physical part.
Premsai Sainathan 23:08
And once you’re able to do that, what are the kind of derived value you see in terms of for your manufacturing plant, for your customers, and for the different teams and functions at Gerdau.
Marco Aurelio de Andrade 23:32
We can explicitly this kind of value for each team which seems has its valuable information right, as sincere I can give some examples by an engineering perspective. And I have some products with the kind of quality problems that stopped in the quality assurance area. Which products it’s then I will. We will not need to to search it. I will, I will have the ability to allocate the logistics errors to, hey, this, this piece is within my production line, but it’s a block. The block, the block analysis product. You have to start in the right place so the production can make, doesn’t have a margin to make an errors. You know, it’s like a keeping over the product line, as a product line where we have this critical product that’s coming from, from an obligation process, from a critical, critical customer, a new customer. For example, we have to know exactly which part of the process is so I can reschedule it correctly. And after this, this schedule that we will have to involve the logistics to move the piece. Then it has to be there. We need to know where the piece is. And from SOP perspective, it’s about the times that the product lines takes and which site they takes. So we can have one quality over the pointing system of mas systems, mis systems, and now for controlling area, we can have the detailed we okay the work, capital of the of the each products, line in details, detail for what really isn’t within the site. So we have a lot of values generated, and from a commercial point of view, for the that impacts directories customer, we can have an assertive, assertive uncertainness in the schedule process, the also the delivering, delivery schedule for the customer.
Premsai Sainathan 26:10
Wow. This is interesting. So I think there is, this kind of gives me the perspective of what you meant by, you know, marrying the digital with the physical. Because, you know, you already have the digital laid out, and now you’re actually matching the physical, physical with the with the digital. And what you’re really trying to do here is you are trying to ensure that there’s a proactive approach, right? So before you know that something is idling, or before something is going to reach the shipping point, you will now have the data to actually schedule what should happen next and do it definitely so, because you now know exactly where that particular component is lying in the process.
Marco Aurelio de Andrade 27:02
You know, the data which we are already had, we had no how much each piece cost, but the hook that brings the physical to the digital, it’s, it’s like a safety on possible problems that can happen. So we know we have on the palm of our hands the information like this piece, as it’s hooking with the system, and you have real insurance. It’s within this item.
Premsai Sainathan 27:37
Marco, you also mentioned one thing in the beginning, which was about the safety of the item. So can you tell me a little bit about this aspect in the consideration, when you were implementing visibility?
Marco Aurelio de Andrade 27:51
With the kind of information that we have, we doesn’t do it, for example, right? We don’t need to to expose a person to search for items, you know. So we we can check system, system in the system, where the the item is. So we have to expose less our work is searching for items. You know, we have a premises from from safety perspective, that the less you expose the person to the to this doing a working area, it’s the less is, the less money for our incidents. Right?
Premsai Sainathan 28:43
Marco, this was fascinating, because tracking is not something new when it comes to assets within the facility, but your journey of evaluating the technologies that avail that was that was that were available in the market, the fact that passive did not really work for you, and you had to actually use sensor which were really enabled and to provide you with active monitoring. And all of the data points, the reports, the analytics that you are looking at, and merging all of this physical data and insights with your digital I think, puts you in a place where you’re truly transforming the manufacturing supply chain from right, from the part where your production starts right, and, of course, delivering the customer experience, which seems really matter to you, which is delivering these products as committed when you’re on a make to order models or. Uh, by leveraging the power of visibility. So Marco, thank you so much for explaining your experience and journey with implementing supply chain visibility in a manufacturing supply chain, we got some wonderful insights from you. So thank you for your time, and look forward to talking to you soon.
Marco Aurelio de Andrade 30:18
Thank you, Prem. All right, talk you to you soon.
Scott Mears 30:22
Hi, my name is Scott Mears, and I’m one of the hosts of the Supply Chain Tech Podcast with Roambee. On this podcast we talk to supply chain heroes from around the world about everything, ranging from the disruptions related to supply chains, their personal experiences with tracking technologies, strategies to build resilience, and much, much more. We already have some recommended videos for you to the side of me, and if any of this sounds interesting to you, do subscribe to our Youtube channel and hit the bell icon so you don’t miss another Roambee video. I’ll see you next time.